Walking into the Y Warehouse Factory | Visiting the Gorgeous "Birth" of Watches
2023-08-22
Walking into the watch factory, the spotless ground, white coats and white hats everywhere, and the constant temperature and dry environment make people feel like walking into a hospital. The entire workshop is clean and dust-free, and the operators complete the assembly and debugging of watches rigorously and meticulously. As the final stage of watch manufacturing, watch assembly is also an important link that affects watch quality. Next, the editor will take everyone into the assembly line to see how a watch is made!
The gorgeous "birth" of brand watches
The composition of a watch can be divided into six parts: case, dial, movement, hands, strap and buckle. In the assembly workshop, these accessories will go through a series of processes such as IQC-clean accessories warehouse-dust-free assembly workshop-quality inspection room-finished watch warehouse, and finally form a watch.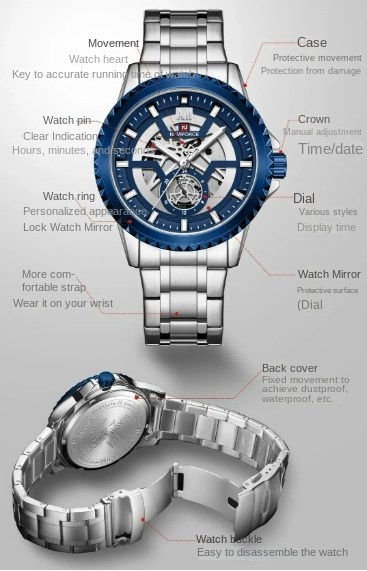
1.IQC (Incoming Quality Control: Incoming Quality Control)
Parts such as the case, dial, movement, and back cover that have been precision-manufactured, polished, and electroplated require a comprehensive "physical examination" before entering the assembly workshop to ensure product quality. Generally, the stricter the IQC quality inspection, the higher the quality of the watch. Therefore, in the IQC workshop, the staff not only need to use specific calipers to measure whether the outline dimensions of parts such as watch cases are qualified, but also check the appearance of parts for defects and screen out unqualified products. Parts that have been fully inspected and qualified are sent to the dust-free parts warehouse through the transfer window, waiting for further assembly.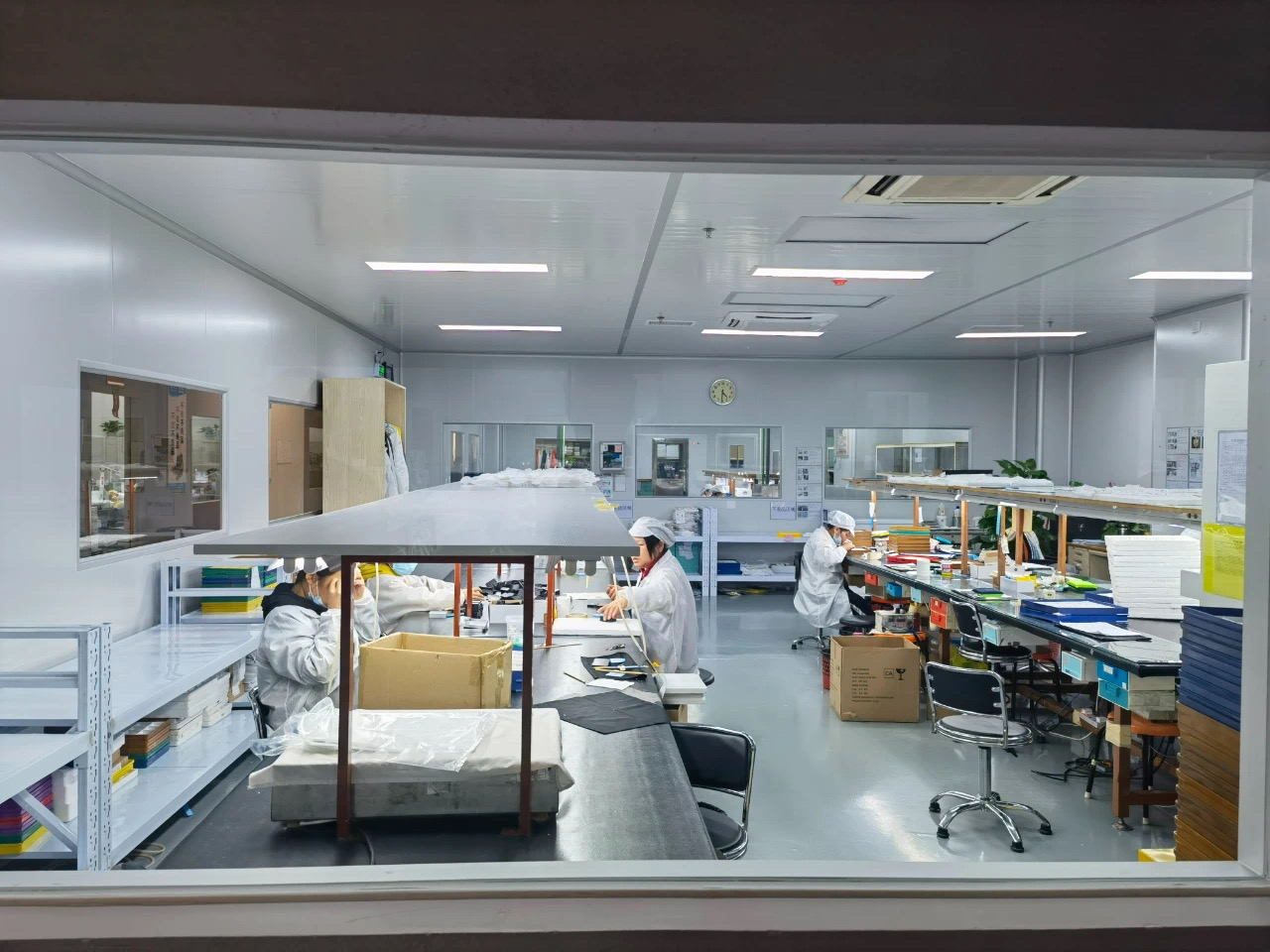
2. Dust-free parts warehouse
In the dust-free parts warehouse, the parts that pass the inspection will be managed according to the corresponding categories.
3. Dust-free assembly workshop
The assembly of the various parts of the watch is done here. It should be noted that the staff have to pass through a small room as airtight as an elevator room - the air shower room, before entering the dust-free assembly workshop. This is to reduce the dust particles brought by the entry and exit of personnel and keep the assembly workshop clean. In the dust-free assembly workshop, workers wear white overalls, slippers on their feet, and rubber finger cots on their fingers. Like a surgeon, they concentrate on assembling and adjusting the small parts of the watch. , watch hands, and the head are all in place and "placed" well, a watch is completed. And because the parts of the watch are fragile and small, the staff needs a lot of patience, and every operation must be extremely precise.
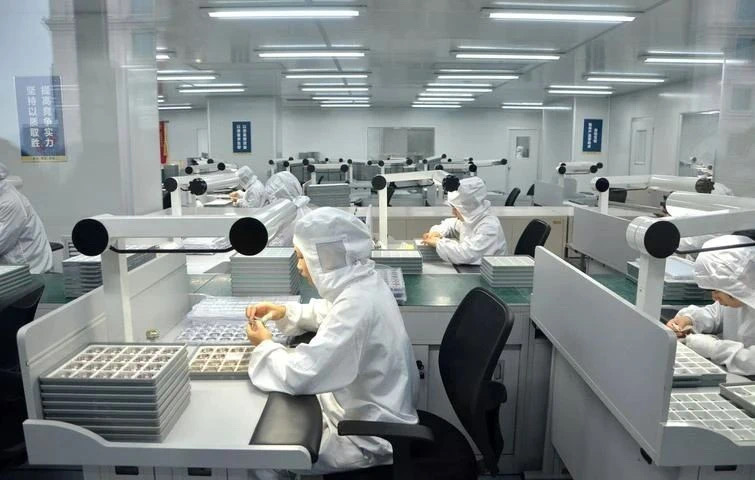
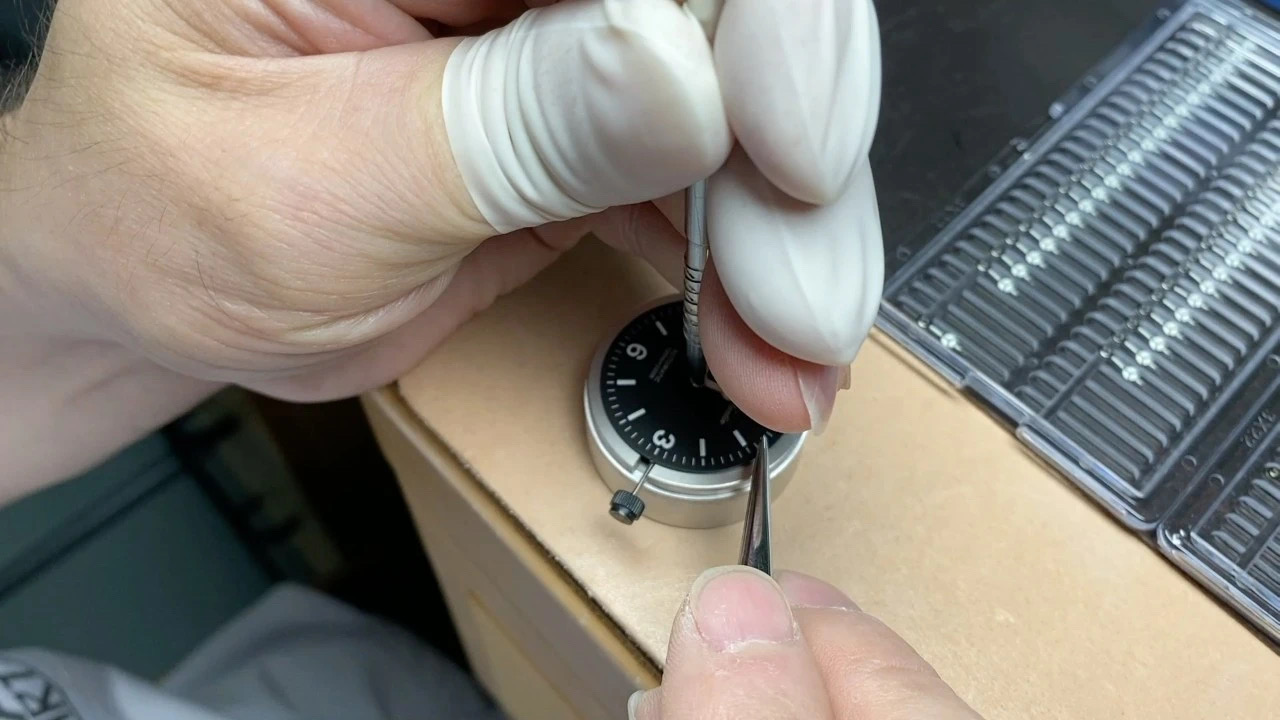
*The staff is installing the hands
4. Quality inspection room
Is it over after the assembly is completed? of course not. The assembled watch also needs to undergo a secondary quality inspection. The focus of the inspection is mainly whether there are scratches, stretch marks and other defects on the appearance of the watch case and watch head, followed by the test of watch functions, real water test, travel time accuracy, whether the pointer is aligned and whether the rotation is smooth, strap tension test, watch With bending test, aging test, etc. After the second screening, qualified watches can enter the finished watch warehouse and wait for outbound sales.
Quality Inspection Room
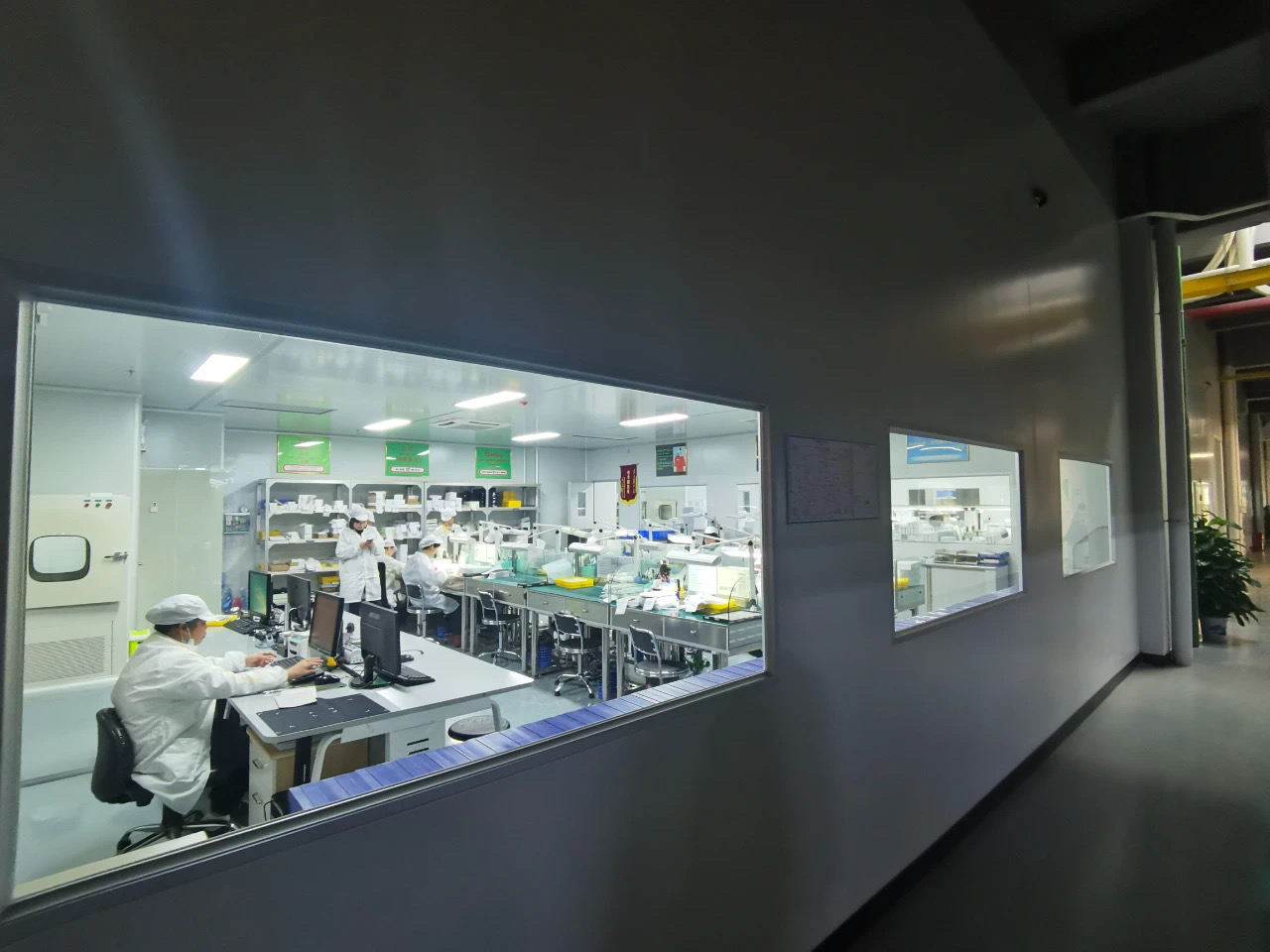
Real water waterproof test
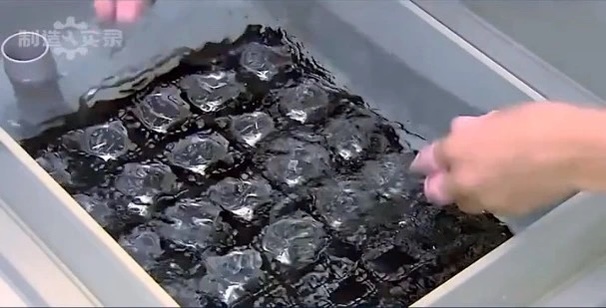
*Scale stress test
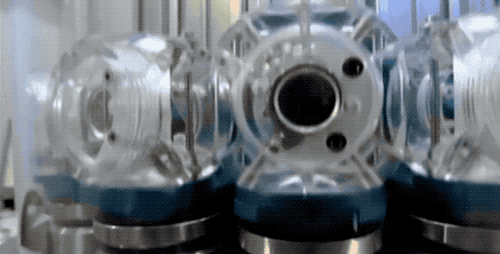
Y Warehouse Watch Factory
The birth of a watch is more complicated than imagined, and so many process steps are required just for watch assembly. In addition, in order to ensure the quality of the finished watch, during the watch assembly process, the components need to undergo multiple product inspections, and the watch components are small, with many types, and the defects are subtle and difficult to detect. It has become extremely challenging to improve watch quality inspection efficiency and yield while reducing costs as much as possible.
Faced with the problem of many types of parts and defects like a watch factory, Y Warehouse Technology's intelligent manufacturing solution can combine the actual quality inspection needs to provide AI quality inspection solutions for multiple different parts, focusing on the contour measurement of watch parts , defect detection, etc., using advanced technologies such as machine vision, AI, and sensors, combined with the Sixth Mirror algorithm custom library, to realize intelligent detection of surface defects on key components such as watch cases and dials, greatly improving the efficiency of assembly quality inspection , to help watch factories realize the transformation and upgrading of "smart inspection".
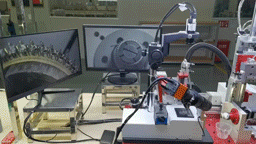
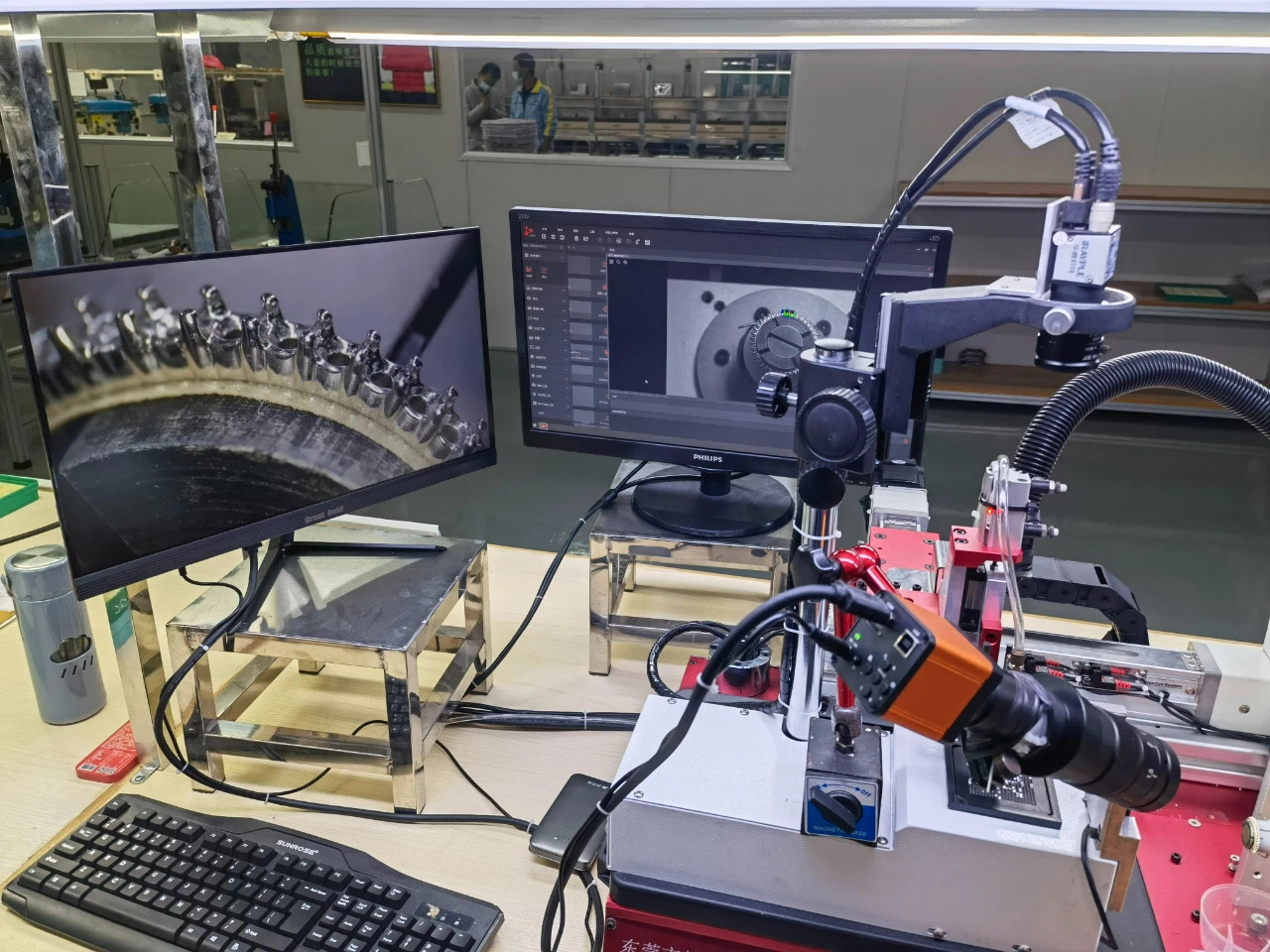
Through the real-time intelligent detection and analysis of the surface defects of parts and components, the demand for highly accurate and high-efficiency refined inspection can be realized, the efficiency and level of quality inspection can be improved to a certain extent, and the control of product quality by production managers can be strengthened to achieve early Early detection can effectively save inspection costs and repair costs, and help manufacturing companies further reduce costs and increase efficiency.
The tour of the watch factory is coming to an end, and we will go to more factories in the future to explore the integration and development of more industries and AI, so that AI applications can flourish everywhere.
The gorgeous "birth" of brand watches
The composition of a watch can be divided into six parts: case, dial, movement, hands, strap and buckle. In the assembly workshop, these accessories will go through a series of processes such as IQC-clean accessories warehouse-dust-free assembly workshop-quality inspection room-finished watch warehouse, and finally form a watch.
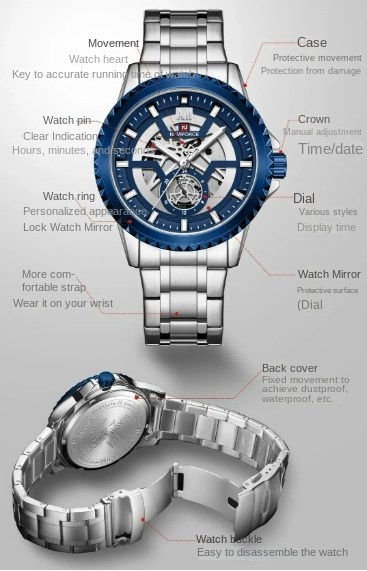
1.IQC (Incoming Quality Control: Incoming Quality Control)
Parts such as the case, dial, movement, and back cover that have been precision-manufactured, polished, and electroplated require a comprehensive "physical examination" before entering the assembly workshop to ensure product quality. Generally, the stricter the IQC quality inspection, the higher the quality of the watch. Therefore, in the IQC workshop, the staff not only need to use specific calipers to measure whether the outline dimensions of parts such as watch cases are qualified, but also check the appearance of parts for defects and screen out unqualified products. Parts that have been fully inspected and qualified are sent to the dust-free parts warehouse through the transfer window, waiting for further assembly.
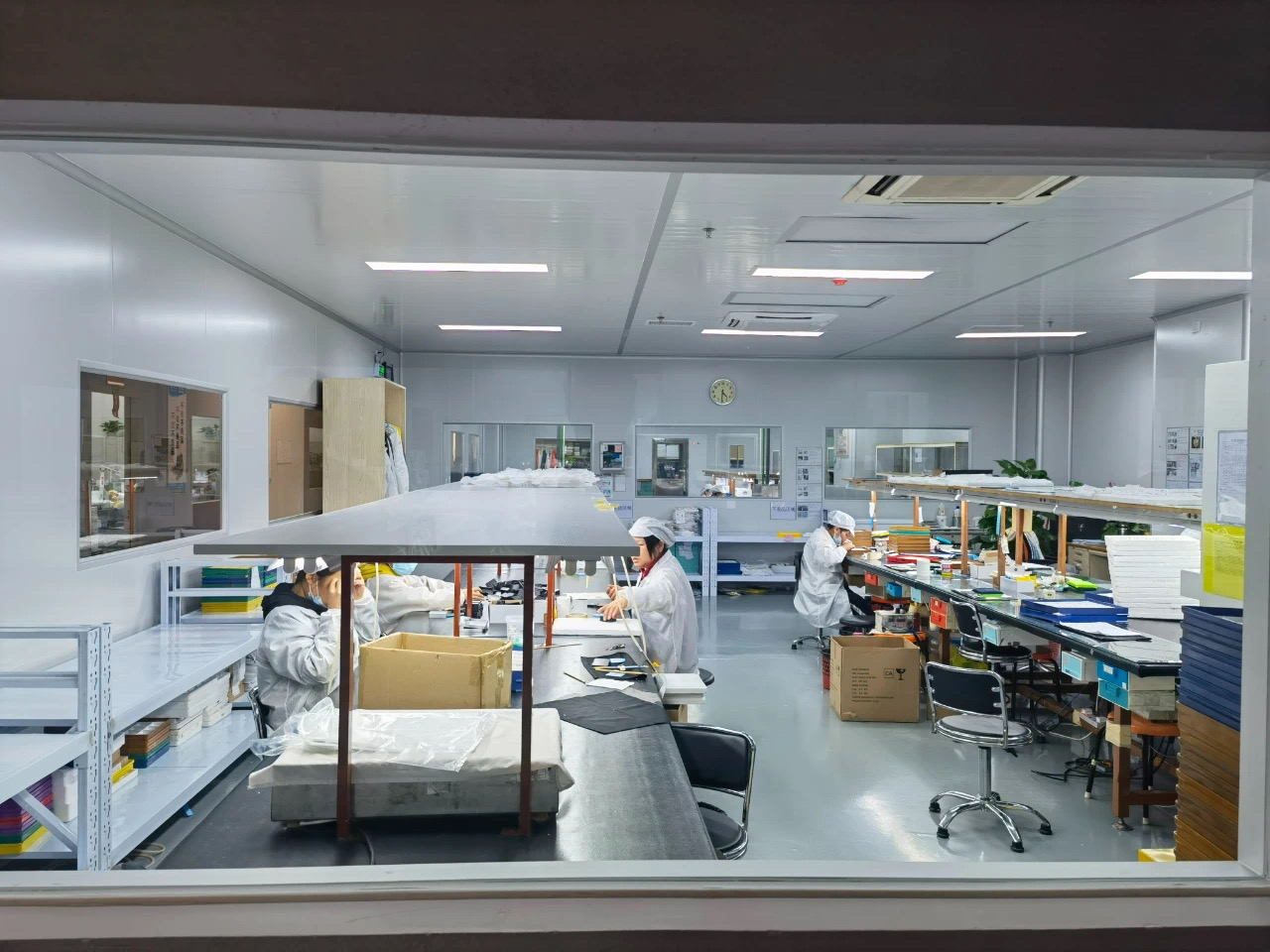
2. Dust-free parts warehouse
In the dust-free parts warehouse, the parts that pass the inspection will be managed according to the corresponding categories.
3. Dust-free assembly workshop
The assembly of the various parts of the watch is done here. It should be noted that the staff have to pass through a small room as airtight as an elevator room - the air shower room, before entering the dust-free assembly workshop. This is to reduce the dust particles brought by the entry and exit of personnel and keep the assembly workshop clean. In the dust-free assembly workshop, workers wear white overalls, slippers on their feet, and rubber finger cots on their fingers. Like a surgeon, they concentrate on assembling and adjusting the small parts of the watch. , watch hands, and the head are all in place and "placed" well, a watch is completed. And because the parts of the watch are fragile and small, the staff needs a lot of patience, and every operation must be extremely precise.
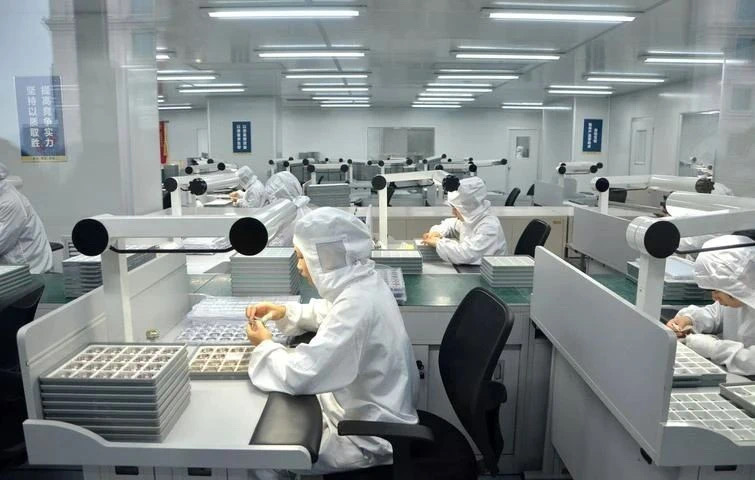
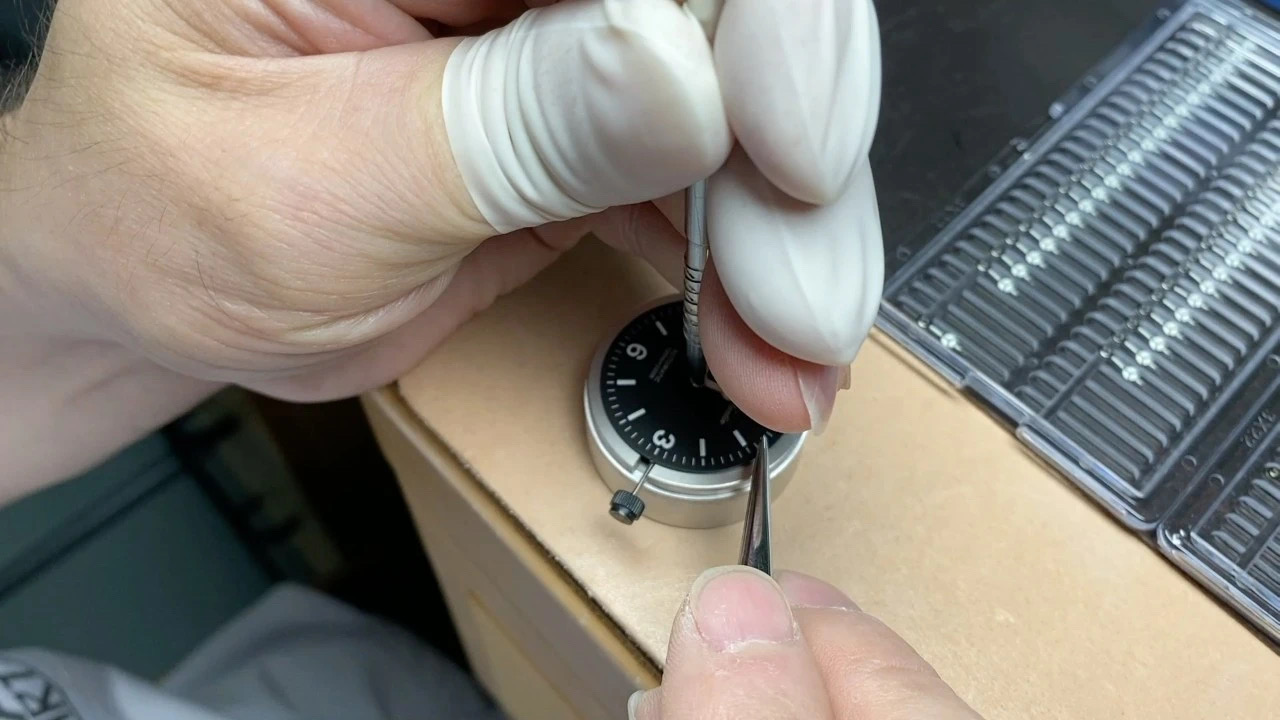
*The staff is installing the hands
4. Quality inspection room
Is it over after the assembly is completed? of course not. The assembled watch also needs to undergo a secondary quality inspection. The focus of the inspection is mainly whether there are scratches, stretch marks and other defects on the appearance of the watch case and watch head, followed by the test of watch functions, real water test, travel time accuracy, whether the pointer is aligned and whether the rotation is smooth, strap tension test, watch With bending test, aging test, etc. After the second screening, qualified watches can enter the finished watch warehouse and wait for outbound sales.
Quality Inspection Room
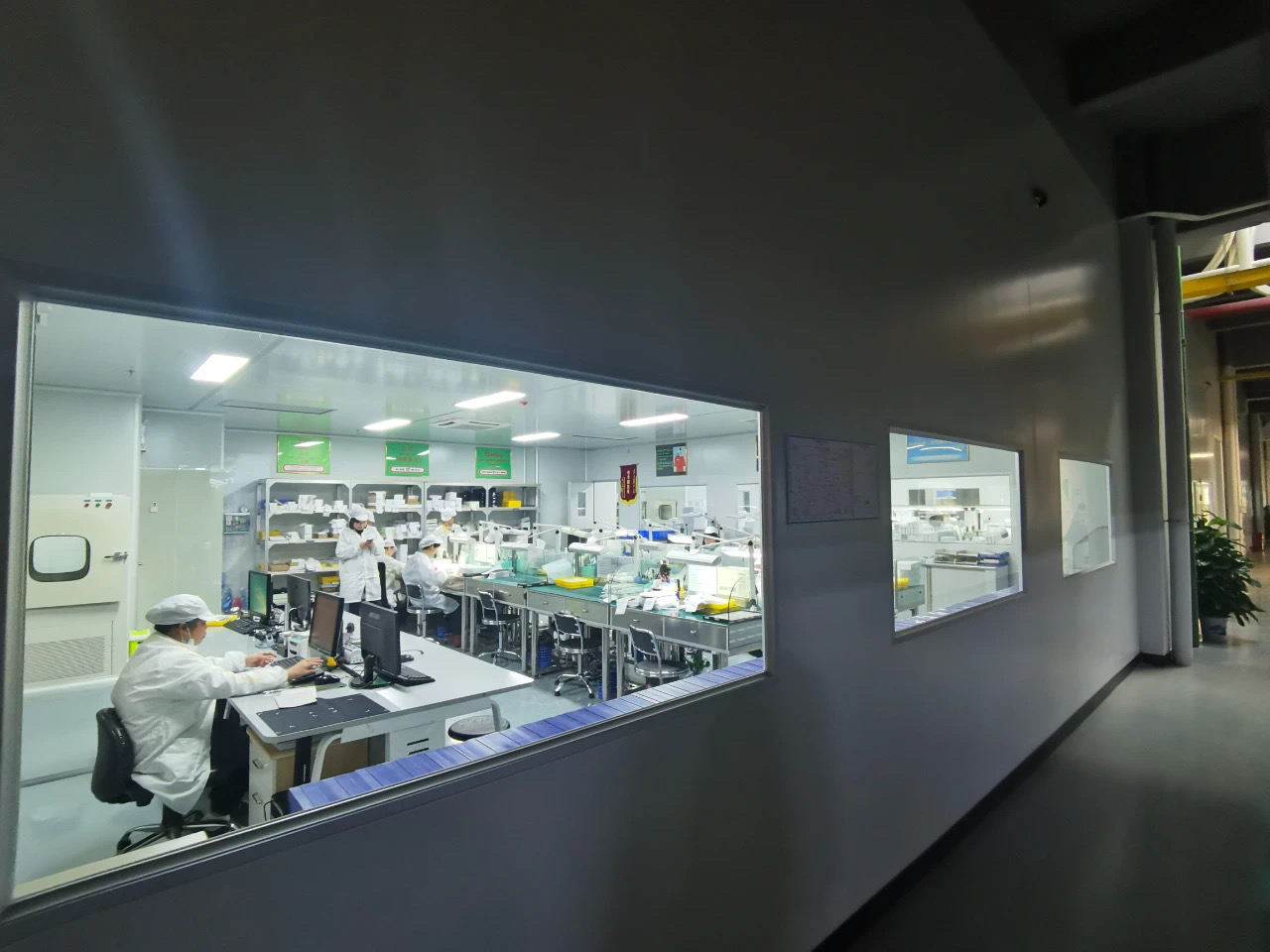
Real water waterproof test
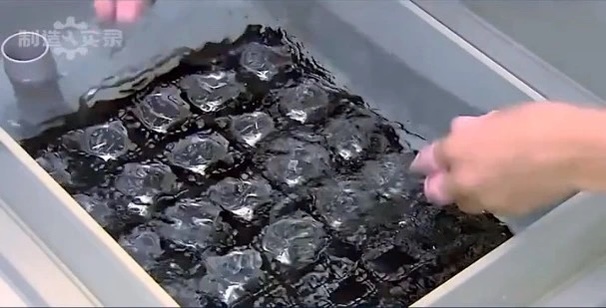
*Scale stress test
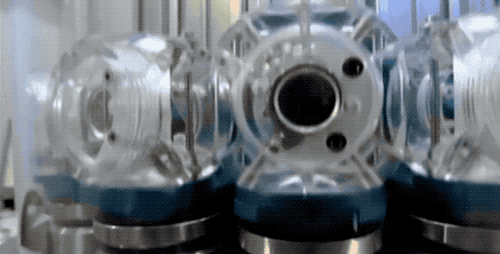
Y Warehouse Watch Factory
The birth of a watch is more complicated than imagined, and so many process steps are required just for watch assembly. In addition, in order to ensure the quality of the finished watch, during the watch assembly process, the components need to undergo multiple product inspections, and the watch components are small, with many types, and the defects are subtle and difficult to detect. It has become extremely challenging to improve watch quality inspection efficiency and yield while reducing costs as much as possible.
Faced with the problem of many types of parts and defects like a watch factory, Y Warehouse Technology's intelligent manufacturing solution can combine the actual quality inspection needs to provide AI quality inspection solutions for multiple different parts, focusing on the contour measurement of watch parts , defect detection, etc., using advanced technologies such as machine vision, AI, and sensors, combined with the Sixth Mirror algorithm custom library, to realize intelligent detection of surface defects on key components such as watch cases and dials, greatly improving the efficiency of assembly quality inspection , to help watch factories realize the transformation and upgrading of "smart inspection".
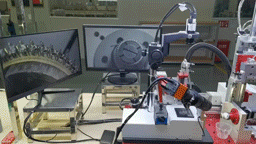
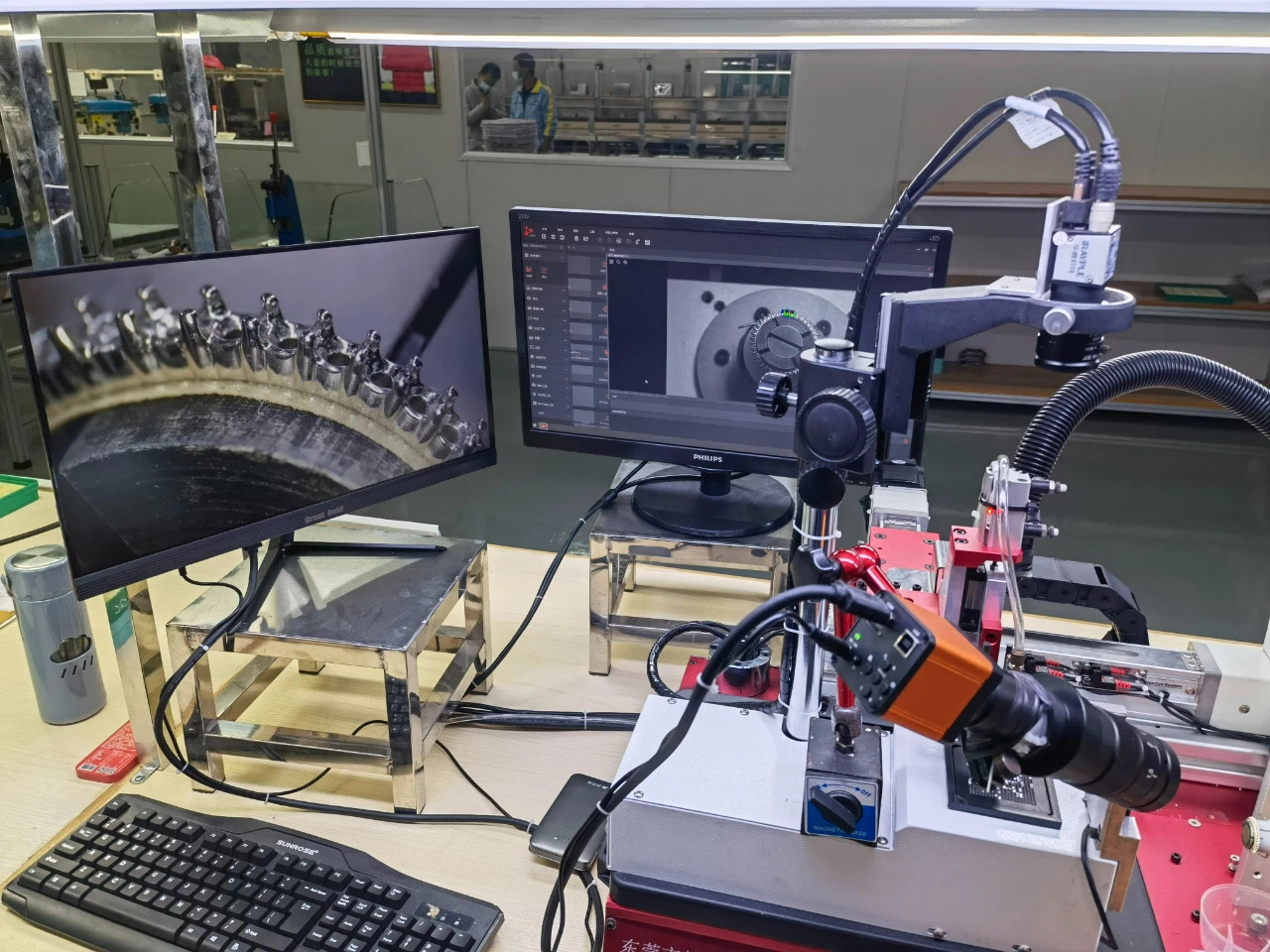
Through the real-time intelligent detection and analysis of the surface defects of parts and components, the demand for highly accurate and high-efficiency refined inspection can be realized, the efficiency and level of quality inspection can be improved to a certain extent, and the control of product quality by production managers can be strengthened to achieve early Early detection can effectively save inspection costs and repair costs, and help manufacturing companies further reduce costs and increase efficiency.
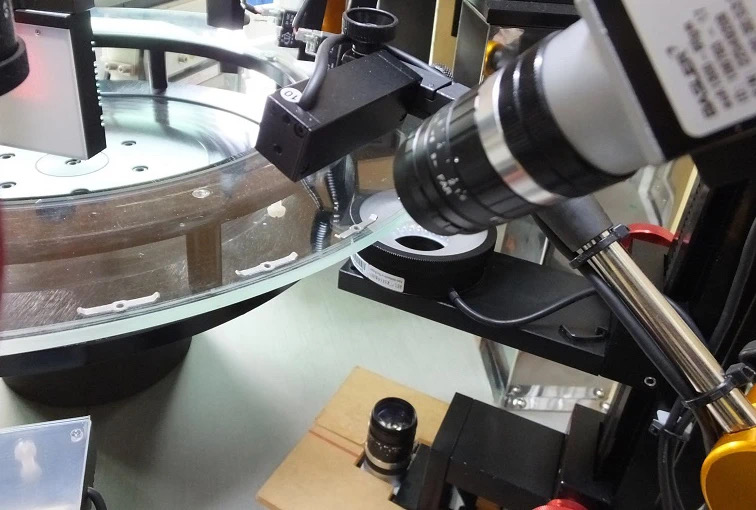